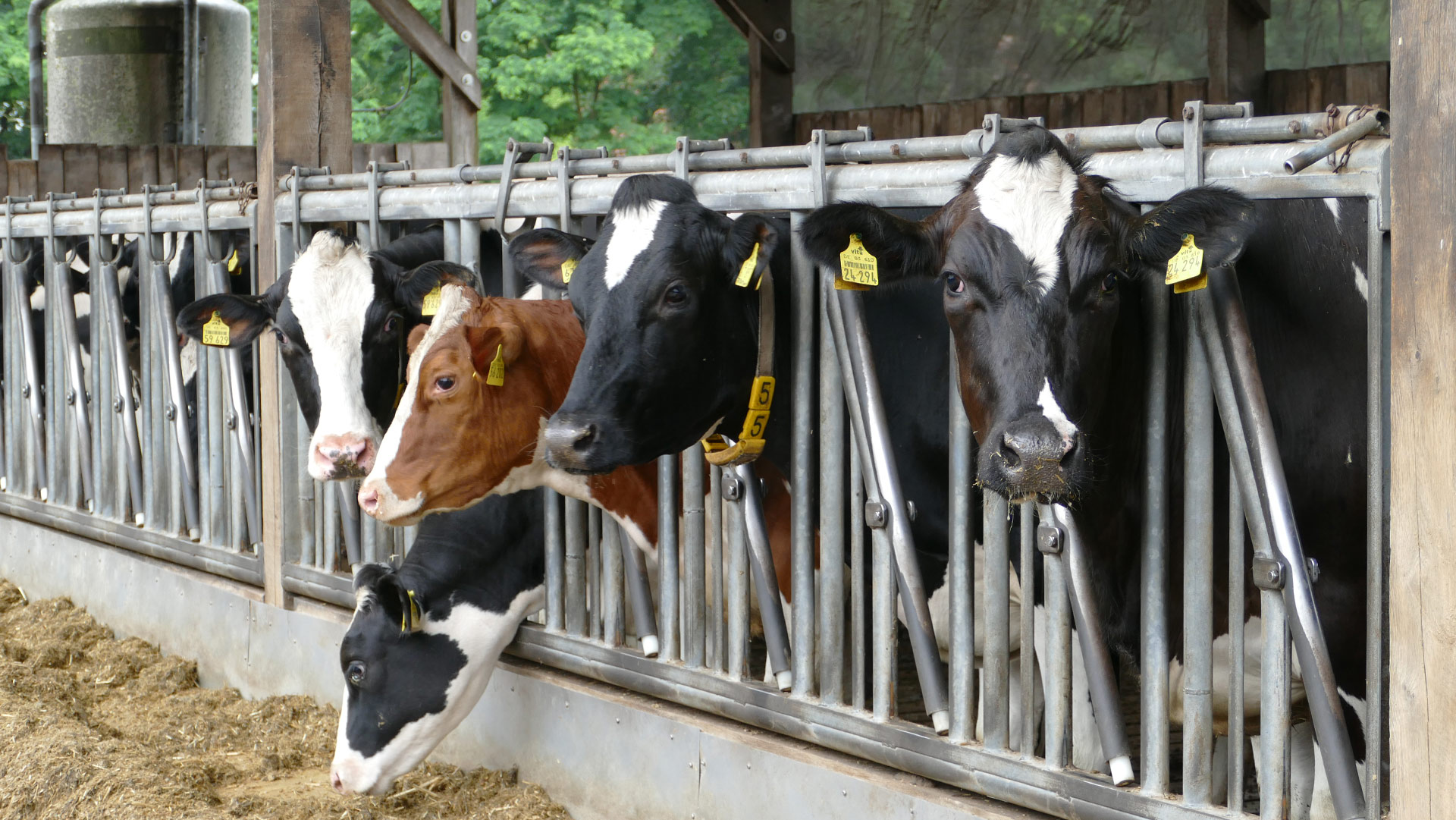
Mixer wagons à la carte
Questions about our mixer wagons
Questions about the technology we put in our mixer wagons and our equipment.
EDS, discharge options, RAEX hard surfacing? We would like to use this section to introduce you to our feeding equipment and the terms we use for our mixer wagon equipment:
Vertical mixing marvels - but why exactly?
Vertical mixer wagons boast mixing augers that virtually “stand” inside the mixing vessel. Their rotation moves up the feed from bottom to top and causes it to slide down on the sides before transporting it upward again. This design allows for a discharge of the feed on both sides that is relatively smooth and even. Additional discharge options are conceivable depending on thecustomer's requirements. The arrangement of the auger(s) even makes it a snap to break up silage bales. This feature, among others, has earned vertical mixers the reputation of being particularly sturdy and versatile.
Discharge options - luxury or agony of choice?
BvL truly confronts customers with an agony of choice as they can - depending on their type of mixer wagon - opt for discharge at the front or at the rear, on the sides, at the rear on the corner or discharge in combination with a cross conveyor, feeding chute or elevator. But, there is a good reason behind this plethora of choices. No farm, barn, feed alley or feed through is like the other. It is our goal to create discharge options that are optimized to accommodate any and all of these different conditions.
If, for instance, the feed alley is particularly narrow, but the customer needs to discharge the feed on both sides, the option for a discharge at the rear in the corners is preferable to discharge on the sides of the wagon. If there is an upturn in the trough area, customers are best suited with, for instance, an elevator capable of transporting the feed up and over this upturn..
Our local representatives/dealers help the farmer find the system that fits the requirements of their particular operation best. The product descriptions of our individual mixer wagons provide you with a quick overview of all possible discharge variants and their extra options.
Preserving the structure in the feed is key
The power mixing auger forms the core element of every V-MIX mixer wagon. It conserves the structure of the load inside the mixing hopper to the highest degree possible. This level of preservation is ensured by its particularly gentle and smooth mixing process.
The power mixing auger can be optimally adjusted to various types of feed by adjusting the knives. The design of the vertical power mixing auger is adapted perfectly to the shape of the mixing hopper - as small as possible, but as large as necessary. This design makes it possible to utilize the full volume of the mixer wagon - regardless of the tank volume - without the need to cut back on the required quality of the mixture. This helps save the farmer / the business both time and money.
Front and rear attachment possible
Yes, the cross conveyor as an add-on to the mixer wagon is available in different sizes. Depending on the mixer model used, it can be attached at the front or the rear of the feed mixer wagon. The conveyor belt is available in different widths and even with speed control to provide for a feed discharge that is as targeted as possible.
Another option is to arrange for a side shift of the cross conveyor: With the conveyor retracted and extended, the wagon can, respectively, traverse narrow entry ways and barn alleys and dispense the fed close to the feed alley.
Power to spare for large wagons
BvL's Powershift gearbox is a reduction gear with integral hydraulic clutch. This transmission allows the operator to start in a low gear and shift to maximum mixing speed under load. The strain on the entire drive train – from the tractor to the mixing auger - is minimized thanks to the reduced power input. This proves particularly helpful when dealing with large feed quantities.
Our extra large Giant series (with tank volumes ranging from 40 to 46 m3) comes standard with BvL's 3-speed Powershift reduction gearbox (powershift transmission). Customers selecting our trailed V-MIX mixer wagons can - depending on the size of the wagon / the power of the tractor - choose an optional reduction gearbox with Bowden cable operation and hydraulic shifting or a 2-speed Powershift reduction gearbox (powershift transmission).
Longer life for the mixer
For all V-MIX mixing wagons BvL offers the option of adding a stainless steel lining.
What is the point? Lining your mixer wagon with high-quality stainless steel (1.4301) may extend its service life depending on the stress you put it through and the feed you use with it.
Our custom-made solutions are tailored to meet the specific needs of each farm and the livestock it houses. Our experts will be happy to provide interested customers with a personal consultation.
Superior mixing quality thanks to sharp edges
The edges on the flights of a mixing auger should remain sharp at all times to achieve the desired mixing quality. If they have become round, the edges on the flight will allow the feed to slip down, resulting in a less than optimal flow of material. Our BvL mixing augers are made of high-quality steel (S355).
Subsequent hard surfacing of the mixing auger flights with BvL RAEX 400 re-sharpens the edges and lifts up the feed to the extent necessary to achieve an optimized and homogeneous mixture..
Proper condition for optimum mixing
The blades fitted on the mixing augers of the mixer wagon should always be close to perfect condition. This is the only way to ensure the best possible mixing process. New blades on a mixing auger reduce the mixing time by approximately five minutes or more per mixing cycle. If you run up to two mixing cycles per day, this means that you may easily save more than €4,000/year.
Our knives are made out of top-tier quality material (40MnB4). The blade is induction-hardened, and the knife can absorb tremendous forces - without breaking. The standard packing plate provides added support and increases stability even further.
Allowing for distribution with perfect precision
EDS stands for Exact Dosing System. As the acronym suggests, this patented system provides for an exact and even dosing of the feed contained in the mixer wagon.
Best of all, there is no need for a conveyor belt. Arranged asymmetrically towards the center of the hopper, the discharge openings are positioned such that the feed - exiting the radius completed by the mixing motion - can be deposited in a loose swathe on the widest point of the mixer wagon, i.e. on the side. The added benefit is that the feed cannot be run over. The entire distribution is fast and even.
No overflow
The V-MIX Plus comes standard with a welded-on anti-spill ring. Designed as a double-tubular construction, the anti-spill ring keeps the feed from spilling over the edge of the hopper while being broken up and mixed. In addition, the design of the anti-spill ring adds tremendous extra stability to the mixing hopper by forming a finishing piece to the hopper.
Customers who prefer a more flexible anti-spill ring can opt for BvL’s Vario ring. This patented anti-spill ring is suspended from chains. It “floats” on top of the mixed material and, among other things, keeps round bales from becoming jammed between mixing auger and anti-spill ring. This is exactly the use case for which this ring is best suited.
Self-loading eliminates the need for a loading vehicle
Save an entire loading vehicle – this is exactly the purpose for which we engineered our self-loading mixer wagons. As their initials suggest, the two models of BvL’s self-loading mixer wagons offer different sets of capabilities:
The L and LS Pro self-loader models of the V-MIX Fill Plus series feature, respectively, a loading scoop for filling the mixer wagon and an integrated cutting unit. They may offer the farmer a great alternative - depending on their vehicle fleet and the equipment on their farm. This is because of the ability to have all work steps completed by a single machine. The self-loader V-MIX Fill Plus LS Pro is a genuine Jack-of-All-Trades capable of removing, loading, mixing, and feeding material in a single set of work steps.
Integrated loading scoop in the L version
The self-loading mixer wagon V-MIX Fill Plus L is equipped with a built-in loading scoop that serves as the loading tool, but lacks its own cutting unit. Among other things, the loading scoop can be used to pick up previously cut silage blocks, round bales and other feed components and break up and mix them inside the mixing hopper - ton by ton.
Fortified to handle any daily wear and tear
The conveyor belts mounted on the BvL mixer wagons will stand up to any abuse daily and professional use can throw at them thanks to their rubber belt that has a thickness of 6 mm and sports a double reinforced textile rubber lining.
The two large deflection rollers fitted on the conveyor belt are designed to ensure non-slip operation even in adverse weather conditions. Our conveyor belts owe their smooth and powerful operation to a single hydraulic motor.
Safety for man and animal
We offer premium grade extraction magnets for all BvL mixing augers that are mounted at the top and the bottom of the mixing auger (Magnet-Plus system). Foreign metal objects are attracted by these magnets, preventing them from entering the feed intended for your animals. Perfectly positioned on the lee side of the mixing auger, these magnets extract foreign objects with superior effectiveness. Once caught, metal parts will not be released again in the further course of the mixing process.
And: Better still, they do not hinder the mixing auger in any way from slicing smoothly through the material. It is also possible to mount a catch magnet at the optional feeding chute. It also holds back any foreign objects contained in the feed. The magnet systems are designed to protect man and animal alike - along with the machine.
A useful detail on the BvL mixer wagon!
Available as an add-on, the feeding chutes that can be fitted on the doors are designed to deposit the feed on the feed alley at a slight distance to the mixer wagon. This prevents the feed from being run over during feeding.
Customers can choose between mechanical and hydraulic feeding chutes.
The latter fold from top to bottom or from bottom to top. The hydraulic - down-to-up - chutes are available with individual and combined selection. Operation is automatic for combined selection. When the farmer opens the discharge gate, the feeding chute will extend completely first before the discharge door opens. Conversely, when the feeding is complete, the gate of the discharge opening will close completely first before the feeding chute returns to its original position (transport position). This option lets the farmer work with much greater ease and also represents the more affordable option compared to the individual selection.
So, why is BvL still offering individual selection? There are situations where the feeding chute cannot be extended all the way, but where the gate is still supposed to be opened for discharge. Such situations arise, for instance, in extra narrow barns or when the farmer needs to use different chute positions in different barns. Individual selection makes sense in these cases as it allows the farmer to control the discharge door and the chute separately. Both versions of the hydraulic chute allow the farmer to set the maximum extension angle using a perforated strip. The top-to-down version is commonly used for feeding in troughs. This version is only available with individual selection.